Industrial Hygiene Monitoring
Protect your workers from exposure to hazards. Measure permissible exposure limits with industrial hygiene monitoring.
Monitoring your work site for hazards and contaminants is a vital part of workplace safety. This allows you to know the data, understand what you need to mitigate, and decide what programs & controls you need. Identifying hazardous exposure in your workplace leads to a safer work environment and supports your overall occupational safety program.
Examinetics can help protect your team from occupational exposures, including noise levels and airborne contaminants such as gases, vapors, dusts, fumes, and other related risks.
Workplace Noise Surveys
Noise monitoring is foundational to any hearing conservation program to identify hazardous noise sources and measure employee exposure. A thorough noise study provides the necessary data to ensure your employees’ hearing is adequately protected, and your safety program is compliant with mandatory hearing conservation regulations.
Examinetics’ noise surveys are conducted by certified occupational audiologists and industrial hygienists. Our experts exceed federal noise monitoring regulations, guaranteeing an accurate and comprehensive depiction of noise throughout your facility.
Why perform noise monitoring?
- Initial monitoring is required for new buildings, equipment, and process to establish the needs of a hearing conservation program prior to employees being exposed to noise.
- Change in production, process, or area controls (e.g., removed a wall that block noise from a group of employees)
- Moving or replacement of equipment
- Periodic or repeated monitoring will identify if employees should be in a hearing conservation program
- Provides crucial information in the determination of work-relatedness if an employee has shown a shift in hearing on annual audiometric testing
- Identify employees that do not meet the OSHA criteria for inclusion, and can be removed from hearing conservation program.
OSHA 1910.95(d)(1)(i) states “The sampling strategy shall be designed to identify employees for inclusion in the hearing conservation program and to enable the proper selection of hearing protectors.”
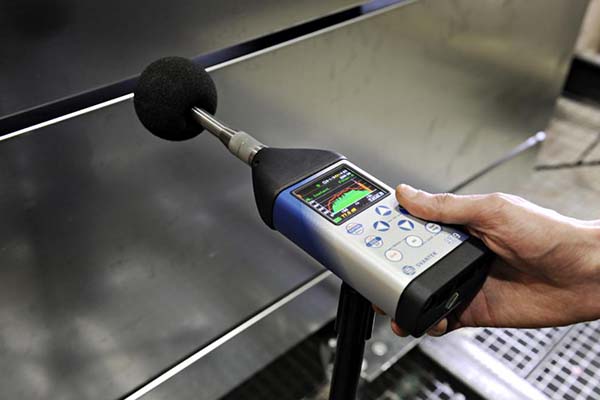
We can meet all your noise monitoring needs using the following instruments:
- A sound level meter is used to take targeted area and process measurements. The readings will reveal how intense noise is in a particular area and is a useful tool for identifying operational noise levels from specific machines, tools, processes, and equipment.
- A noise dosimeter is a small, wireless microphone worn by an employee to measure cumulative noise exposure over the course of a workday. A dosimeter records noise levels throughout the day and will calculate a time-weighted average (TWA) exposure. Personal noise dosimetry is the most accurate and appropriate tool for measuring noise exposure of non-stationary employees with various tasks and work areas.
Reporting:
- Written summary of our findings
- Targeted sound level meter and personal noise dosimetry results
- Outline federal regulation requirements
- Best practice hearing conservation recommendations
- Hearing protector assessment to ensure adequate employee protection (if applicable)
Air Sampling
OSHA and other regulatory agencies have air monitoring requirements to protect workers from health risks due to air contaminants at work. OSHA has defined hundreds of air contaminants including hazardous chemicals, toxic fumes, “nuisance dusts”, and other particulates such a silica.
Effective sampling strategies need proper planning to ensure the most comprehensive evaluation. Examinetics has highly qualified industrial hygiene and lab partners to help you get the air quality data you need to make informed decisions on workers’ exposure and what programs and abatement strategies you need.
Why perform air sampling?
- Initial or baseline sampling to ensure compliance with regulatory exposure standards
- Substance-specific standards require that periodic sampling be performed on a regular basis, such as monthly or quarterly.
- Whenever there has been a production process, control, or personnel change, or when there is reason to suspect other change which may result in a new or additional exposure. (e.g. change in ventilation systems, isolation barriers)
- Decide proper personal protective equipment (PPE)
- Assess the effectiveness of hazard controls
- Find the source of leaks
- Protect against future liability
Air Sampling can identify:
- A substance’s concentration over different time frames
- The level of multiple substances in the air as a result of emissions from a single source or multiple sources
- A substance’s concentration at a wide range of locations
- Contaminants deposit in greatest quantities
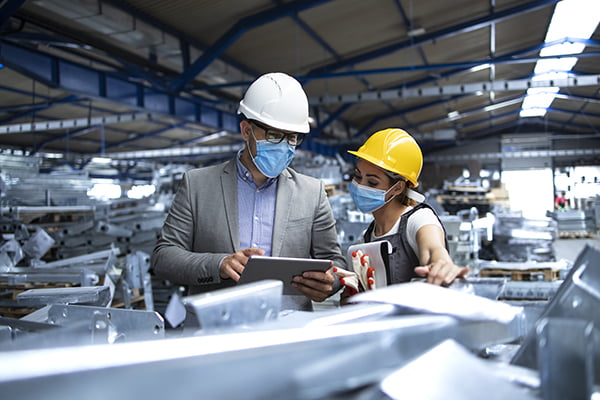
We can meet all your facility needs:
- Area air sampling measures air quality in certain areas of your workplace to give insight into general exposure. This is commonly used for locating contaminant sources. The process takes samples of air from the ambient environment. Ambient air sampling devices are generally larger and have high flow rates, so they can sample a large volume of air in a short time.
- Personal air sampling measures personal exposure to airborne hazards and shows how vulnerable specific job tasks may be. In personal air sampling, a worker often puts on wearable sampling equipment, usually over the area several inches from the face, and goes about a typical workday. The equipment captures a representative sample of particles the person comes into contact with.
Reporting:
- Summarized lab report findings
- Sample data and exposure summary
- Suggested air quality improvements